GPL 10000
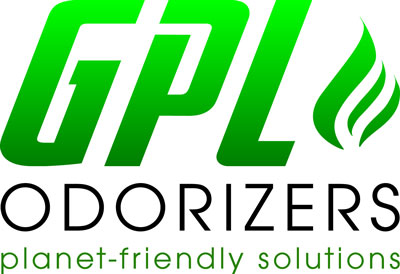
The GPL 10000 odorizer is an eco-friendly odorant injection system used to odorize gas. The odorizer meets the demands of nearly all pipeline applications and ideal for high-volume and high-pressure applications. The 10000 is ideal for high-volume and high-pressure applications. With a 100:1 turndown ratio, the system injects precise quantities (0.2% accuracy) of liquid odorant across the entire operating range, in both continuous and batch modes.
About GPL Odorizers
GPL Odorizers (formerly Sentry Equipment and Zeck Systems) manufactures environmentally-friendly odorant injection systems for natural gas and other gases.
Odorize Gas Differently
The GPL 10000 is electrically driven and hydraulically isolated. Pipeline gas does not actuate the injector, meaning our odorizers do not vent gas to the atmosphere, making this system environmentally friendly. Additionally, since GPL odorizers are self-contained and do not discharge gas, there is improved safety, pipeline gas is saved, and subsequently, odor at the unit is reduced. As a result, there is a reduction in leak call complaints.
The GPL Odorizers also have fewer moving parts than the leading competitive odorization systems, meaning less maintenance over the unit’s life.
What makes GPL 10000 Unique?
What makes the GPL 10000 unique is its dual stroke electrohydraulic pump. A variable speed electric servo motor drives a stochastic mechanism that converts the motor's rotary motion into linear double stroke motion. This provides the force to drive two independent metal Bellows Pump modules. The dual stroke sends the hydraulic fluid into one of the pump modules, compressing the bellows to discharge a fixed volume of the odorant. Simultaneously, hydraulic fluid is withdrawn from the opposite pump module, expanding that bellows and drawing in new odorant for the next injection stroke. This action provides nearly continuous injection flow, a feature not offered by single pump injectors. As the pipeline flow rate varies, the pump motor speed is adjusted to change the time per stroke while maintaining a continuous flow of odorant in the process. Since the motor has the maximum rate of 25 revolutions per minute, fluid flashing, due to acceleration induced pressure drop, is virtually eliminated. Additionally, the Bellows Pump's hydraulic section is completely isolated from the odorant section, and there are no seals or diaphragms to replace in the odorant section of the pumping circuit. The only replacement items are the hydraulic piston seals that have been engineered for high cycle life. When piston seal replacement is required, the drive system is easily isolated from the pump modules by closing the isolation ball valve located on each hydraulic line. The piston seals are captured within cartridge assemblies to allow for quick and easy replacement. The GPL 10000 odorizer uses the state of the art technology for accurate, repeatable, and low maintenance odorant injection.
Features & Benefits
Improved safety
Saves pipeline gas
Environmentally friendly
Lowers leak call complaints
- Few moving parts
low maintenance cost
- Excellent full-range accuracy
- 10-micron odorant filter
- Automatic system shut-off for low odorant supply pressure
- GPL 10000 Datasheet
- GPL General Brochure
- Design Questionnaire
- GPL 10000 Odorization Principle of Operation
Specifications
Weight
194 lb. (88 kg)
Power
Typical: 24 VDC; 0.036 HP; 27.05W
Maximum: 24 VDC; 0.193 HP; 124.8W
Optional: Optional AC and solar
Gas Pipeline Pressure
To 1480 psi (102 bar) maximum
Odorant Blanket Pressure
15 to 30 psig (1 to 2 bar)
Data Logging
Hourly archives with audit trail
Enclosure
304 stainless steel
Odorant Injection Rate, Continuous1
.50–50 cc/min. (.008–.793 gal/hr.) at a natural gas flow rate of .107–10.7 MMSCFH (3029–302990 Sm³/h)
Odorant Injection Rate, Batch
For natural gas flow rates below 100,000 SCFH down to virtually zero flow
Connections
- Myers hub: (3) 3/4 in NPT; (2) 1/2 in NPT
- Odorant outlet, odorant return, vent, odorant inlet: 1/4 in comp
Operating Temperature Range
- 0–140˚F (-18–60°C)
- Optional: Heater assembly available for below 0°F (-18°C)
Hazardous Area Classification
Class I Division 2, Groups C and D
User Interface Options:
- Optional HMI via a serial interface (max. 20 ft. from the unit)
- 10000-configured TechView via Ethernet or Internet (supplied at no charge)
- Serial RS-485 Modbus; Open/TCP Modbus via cell modem
Additional Options:
Wireless modem, battery pack, solar panel, odorant tanks, and containment
1 At injection rate of 0.5# mercaptan/MMSCF (10 mg/m³)
It is the end user's responsibility through analysis and testing to select suitable products and materials for their specific application requirements, ensure they are correctly installed, safely applied, properly maintained, and limit their use to their intended purpose. Improper selection, installation, or use may result in personal injury or property damage.
Options
- Service maintenance package
- Thermoelectric generator
- Odorant pressure control
- GPL Odorization Training Classes
Upgrades to Systems
- Turnkey odorization packages
- Tanks and Containment
- Fiberglass Buildings
- Temporary Odorization or Pickling Units