Many of our products contain electrical components, such as GPL Odorizers odorization systems, and may be used in hazardous areas. Customers may seek out equipment with certain hazardous area classifications or descriptions, such as explosion-proof or intrinsically safe. This warrants further discussion on the difference between intrinsically safe and explosion-proof.
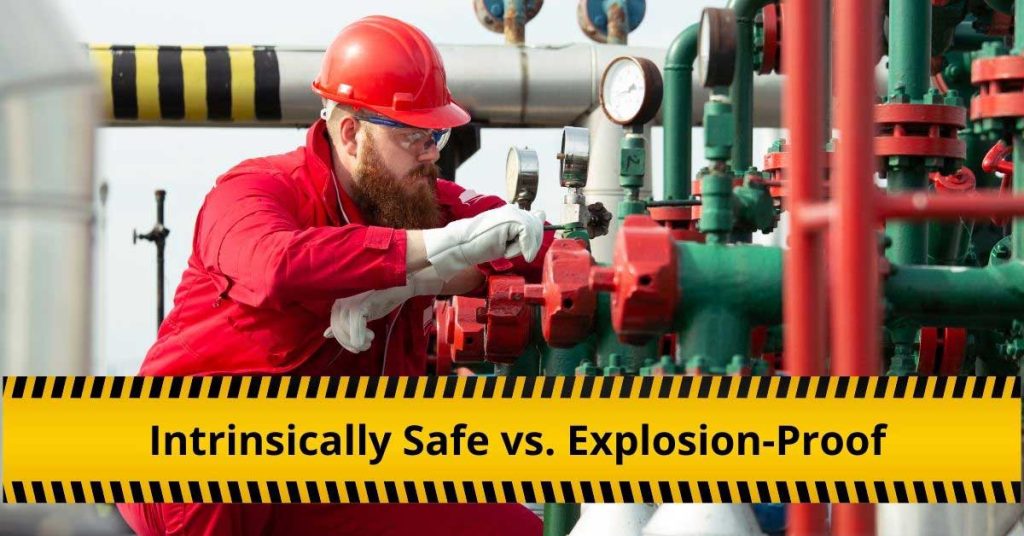
Request More Info
Intrinsically Safe vs Explosion-Proof
At times, electrical equipment must be used or installed in locations where vapors or gases are present. These areas are known as “hazardous locations.” When equipment needs to be installed in these areas, the operator must follow rigid material and design guidelines. The NEC, or National Electrical Code, provides guidelines for electricians, electrical contractors, inspectors, and engineers In the United States. These guidelines are part of the National Fire Code Series and published by the National Fire Protection Association, with updates every three years.
The NEC defines protection techniques equipment manufacturers must use when designing equipment intended for use in hazardous areas. NEC definitions set the parameters manufacturers must comply with for any component to be installed in a hazardous area. These definitions are explosion-proof, dust ignition-proof, dust-tight, purged/pressurized, intrinsically safe, and hermetically sealed.
Most of the equipment we represent used in hazardous locations is either explosion-proof or intrinsically safe.
Explosion-proof
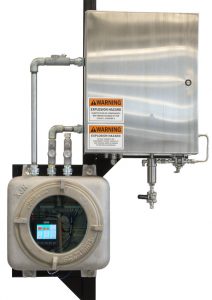
Pictured is a GPL 750 Odorizer with its electronics enclosed in a CL I Div 1 explosion-proof enclosure.
Equipment with an explosion-proof classification doesn’t mean the material will survive a blast. Instead, it means that the equipment is housed or has an enclosure that prevents an internal spark from causing a much more massive explosion. In this case, the cabinet must be engineered to contain any flash or explosion. The housing on this type of equipment is generally constructed of stainless steel or cast aluminum and strong enough to contain an explosion should gas or vapors seep into the enclosure and the internal electronics ignite. The equipment must be designed so that if there is an internal explosion, the external surface temperature does not meet or exceed the ignition temperature of the gases in the equipment’s rated group.
Intrinsically Safe
An intrinsically safe rating means that the electronics or wiring contained within the equipment cannot spark or accumulate enough energy to ignite the gas or vapor at the location. Additionally, the equipment’s surface temperature cannot get high enough to ignite the gas or vapor at the site.
Classifications of Hazardous Atmospheres
The NEC is also a classification tool for hazardous conditions. Many products we sell are typically associated with a hazardous location classification. The following explains what the classification denotes.
There are three types of hazardous conditions or classes:
- Class I – gases and vapor
- Class II – combustible dust
- Class III – fibers and flyings
There are two kinds of hazardous conditions within a class.
With Class I on gases and vapor hazards, the two kinds are:
- Division 1: The gases or vapors are always present at sufficient concentrations to be an explosion hazard.
- Division 2: The gases or vapors may be present, and if they are, they are likely to be in insufficient concentrations to be an explosion hazard.
In Class I, there are four Groups (A, B, C, D), which are classifications of atmospheres by the degree of volatility, with “A” being the most hazardous and “D” being the least volatile group.
- Group A: Acetylene
- Group B: Hydrogen and manufactured gases containing Hydrogen
- Group C: Petrochemicals
- Group D: Petrochemicals (includes methane)
For information on Class II and Class III, download Hazardous location and OSHA Regulation information.
What is the difference between explosion-proof and intrinsically safe? The internals must be engineered to contain an internal explosion and avert a much larger detonation in explosion-proof equipment. The intrinsically safe rating means the electronics cannot spark or create sufficient energy to ignite. In both cases, the equipment’s surface temperature cannot meet or ignite the rated group’s gas or vapor ignition temperatures.
Common Class locations:
Class I Locations | Class II Locations | Class III Locations |
- Petroleum refineries and gasoline storage and dispensing areas
- Dry cleaning facilities where vapors from cleaning fluids are present
- Spray finishing areas
- Aircraft hangars and fuel servicing areas
- Utility gas plants and operations involving the storage and handling of liquefied petroleum gas or natural gas
| - Grain elevators
- Flour and feed mills
- Plants that manufacture, use, or store magnesium or aluminum powders
- Plastic, medicine, and firework manufacturers
- Starch or candy producers
- Spice-grinding plants, sugar plants, and cocoa plants
- Coal preparation plants and other carbon handling or processing areas
| - Textile mills, cotton gins
- Cottonseed mills, flax processing plants
- Plants that shape, pulverize, or cut wood and create sawdust or flyings
|
Very informative.
what’s meant by atex approved ?
ATEX is an EU directive for “Devices intended for use in explosive atmospheres.” The US equivalent is the HAZLOC standard given by the OSHA as classifications of hazardous locations such as explosive atmospheres.