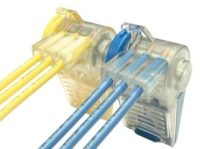
Wire Connector
The PRO-TRACE Wire Connector by Pro-Line Safety Products is ideal for underground splices and connections for tracer wire and other applications not exceeding 300 volts. The corrosion-proof fitting performs better than twist-on connectors and is easier to install.
Wire Connector
The silicone-filled fittings are used to splice or branch-off multiple tracer wires for system continuity. They provide corrosion protection from the below-ground elements and deliver a sealed wire connection system in damp and wet locations. The PRO-TRACE TW Connector meets or exceeds UL standards, and NEC requirements.
Pro-Line Safety Corrosion Proof Wire Connector
- Specially designed for locating wire
- Direct burial rated
- Operative in damp, wet, and submersible settings
- Silicone filled (-40°F to 400°F)
- Waterproof and corrosion proof
- Impact and crush resistant
- 300 volts maximum
- RoHS compliant
- Superior to twist-on or wire nut fittings
- Stronger than 3M of DryConn wire nuts
- Error proof installation